Within the industrial sector, the integration of artificial intelligence (AI) signifies the incorporation of this cutting-edge technology into manufacturing processes, taking them to a new level of automation and autonomy. This transformation gives rise to the creation of smart factories and sophisticated robotic systems. As AI expands to increase productivity and quality, the global landscape anticipates a rise in the prevalence of robotized factories.
The goal of employing AI in manufacturing is twofold: to improve productivity and quality while mitigating production costs. Additionally, AI acts as a proactive guardian against potential hazards such as gas leaks or fires, safeguarding human life.
There are various methodologies for assimilating AI into industrial practices. These range from deploying intelligent robots along production lines to creating deep learning-based computer vision systems for meticulous quality control, to internal data management models based on machine learning algorithms.
Contemporary emphasis is on smart factories equipped with autonomous devices capable of learning independently, cognitively processing, and perceiving their environment. The primary goal, in which AI plays a primary role, is to establish a self-sufficient system capable of solving production problems with minimal human intervention.
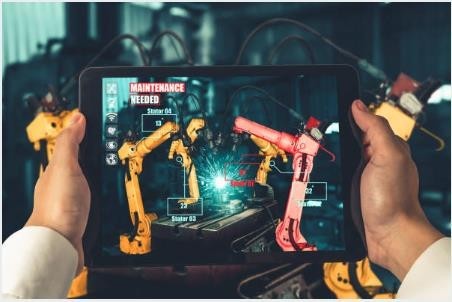
Applications of Artificial Intelligence in Manufacturing
AI plays a crucial role in executing tasks such as welding, painting, assembly, and manipulation, achieving precision comparable to or greater than that of the most skilled human workers. Additionally, AI excels in managing workflows with impeccable efficiency.
Manufacturers can leverage AI to monitor complex processes or machinery in real-time. This monitoring facilitates risk identification and enables predictive maintenance solutions through data analysis. Some applications include:
- Quality Control:
Enables a deep understanding of equipment status, minimizing downtime, and optimizing asset utilization.
- Improvement of Energy Efficiency:
Contributes to increased energy efficiency by analyzing equipment and interpreting vast datasets for optimized supply chain planning, process design, and resource management.
- Packaging and Logistics:
Utilizes the Internet of Things (IoT) for real-time monitoring, optimizing the packaging process through machinery and conveyor belt monitoring.
Benefits of AI in the Industry
- Elimination of Bottlenecks:
In the era of Industry 4.0, traditional bottlenecks are replaced by new opportunities that can be easily identified, analyzed, and exploited.
- Discovery of Hidden Costs:
Through data analysis, manufacturers can discover hidden costs in their processes that often go unnoticed when considering only standard costs.
- Error Reduction:
Manufacturers can identify the root causes of errors, reducing the likelihood of repetition.
- Prediction:
AI has the ability to predict events such as chemical leaks, fires, equipment breakdowns, and component failures.
- Machine Maintenance:
AI-driven machinery can be used for predictive analysis, detecting issues before they occur and providing solutions.
- Information Security:
Manufacturers can now protect valuable information by simplifying access and, at the same time, adding an additional layer of security.
- Time Savings:
AI can eliminate simple tasks, allowing people to focus on their core skills. Additionally, it can speed up production by facilitating collaboration between humans and machines. Although complete automation is not expected with the use of AI, the combination of the “humans plus AI” approach can increase productivity by 30%.
- Identification of New Opportunities:
AI allows manufacturers to better understand customer needs, respond more quickly to market demand fluctuations, and identify new growth opportunities.
Conclusion
Artificial intelligence stands as a transformative force in the manufacturing industry, driving intelligent automation, seamless collaboration between humans and machines, and continuous process improvements. The synergistic adoption of digitization and AI is not just a futuristic concept; it is already a reality for many companies reaping tangible benefits.
Beyond the technical realm, AI provides a deep understanding of customer needs and anticipates market demand, paving the way for unprecedented growth opportunities. In the era of Industry 4.0, it is this adaptability and responsiveness that will distinguish industry leaders.